Mankind seeks to drastically reduce the consumption of fossil fuels. However, the energy density of petroleum products is so high that it is difficult to replace them to power airplanes. For example, the energy density of lithium batteries and 0.4 kW kilos, against 13 km per kg of kerosene. This makes batteries and their weight a major handicap for the distribution of electric planes, especially for medium and long distances, whether it is a private jet or an airliner.
The need to design more environmentally friendly private and liner jets
More and more people are singling out private and passenger jets for their impact on global warming. While aviation contributes only 3.5% to climate housing, compared to 50% for transport in general, public opinion considers it among the main contributors to the worsening of the situation. Of course there is a lot of research going on, and in 2018 Boeing first flew an airliner with 100% biofuel. Still, biofuels are problematic, as in order to produce them, land has to be removed from traditional agriculture, exacerbating the food shortage that already affects hundreds of millions of people.
The development of the hydrogen engine
Another way forward is the development of the hydrogen engine. To be environmentally friendly, hydrogen must be produced either by electrolysis with renewable energies, or with natural gas using carbon capture and storage technologies. Hydrogen can be used in three ways: as a fuel in slightly modified jet engines, to generate electricity through fuel cells and thus power electric motors, which are lighter than batteries. Third, it can be used to produce biofuels.
Airbus zero emission turboprop
On the European side, ACARE (Advisory Council for Aeronautical Research in Europe) has set itself a very ambitious 2050 target which is to achieve a 75% reduction in CO2 per passenger kilometer for new technologies (airplanes / engines) with new operational practices (air traffic management, flight optimization) in 2050 compared to representative aircraft, engines and operations of the year 2000.
The two largest aircraft manufacturers in the world, Airbus and Boeing, have already drawn up plans to equip their planes with hydrogen engines. I’ve written here about Airbus and its plans to develop hydrogen airliner jets, which are slated to enter service around 2035. Boeing already flew an aircraft in 2008 powered by fuel cells powered by hydrogen.
Four years later, the company unveiled the Phantom Eye, an unmanned aerial vehicle (UAV) that runs on liquid hydrogen. It was designed to perform reconnaissance missions of up to four days at an altitude of 20,000 meters. However, Boeing was unable to sell the drone to the military and it is now a museum piece.
Boeing estimates that it will be 20 years before its first hydrogen-powered aircraft come into service. For the time being, the American aircraft manufacturer is thinking more of a mix of solutions, in which biofuels will play an important role.
The biggest obstacle to hydrogen powered flight is the extra weight required to store fuel, whether in gaseous or liquid form. For liquid hydrogen, the challenge will be to manufacture lightweight, vacuum-insulated tanks that keep the fuel below its boiling point of 20 K. The gas carries a greater weight penalty, as the tanks must be built to withstand high pressures of 250 to 350 bar.
Hydrogen requires tanks that weigh four times the fuel they contain!
Measured in megajoules per kilogram, liquid hydrogen offers 2.8 times the energy density of aviation fuel. But in terms of combined fuel and tank weight, aviation fuel has a 1.6 advantage over hydrogen. While aviation fuel makes up about 78% of the combined tank and fuel weight, liquid hydrogen only makes up 18% of the total in current storage designs. To compete with fossil fuels, the fuel weight fraction must reach at least 28%.
Weight and energy density
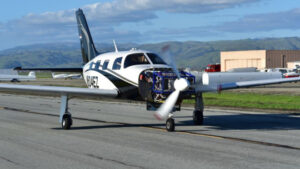
Compared to hydrocarbons, liquid hydrogen has much lower energy per unit volume. One potential solution is a mixed wing-fuselage design.
ZeroAvia will use hydrogen compressed at 350 bar on the fuel cell aircraft it plans to fly in short jumps of 500 nautical miles (about 900 km) or less. But a pressurized storage system requires a much more robust tank and would take up about twice as much space as tanks containing liquid hydrogen. This is not feasible for large airliners carrying 150 or more people on longer flights.
By the end of the decade, ZeroAvia plans to launch a 50 to 100 passenger fuel cell aircraft powered by liquid hydrogen. The tanks would be made from combinations of existing composites and resins. ZeroAvia’s current fuel / tank weight ratio is 11-12% for gaseous hydrogen. The company is currently testing liquid hydrogen tanks with ratios above 50%.
ZeroAvia’s six-seater fuel cell aircraft made its maiden flight in September 2020 in Cranfield, UK. The company claims it is the largest hydrogen-powered aircraft in the world.